Brendan Flood, Director of Distillery Systems at DRAMS, explores the changing role of master blenders in today’s competitive market
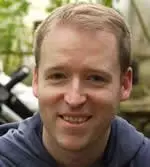
While many whisky drinkers like to imagine that their dram has been produced with strict adherence to centuries of tradition, in truth great blends rely a little more on modern methods than marketing lets on. In the increasingly competitive spirits market it’s a simple truth that a distillery that fails to modernise is one that will fall behind.
Today’s master blenders face challenges that leave no room for inefficiency, driving their craft to become logical rather than purely mystical. And while there are personal qualities and skills essential for a master blender, access to modern technology has become just as vital.
So what does today’s master blender need to create blends that honour whisky’s rich history, while ensuring the distillery’s continued success?
The right blend of skills
The role of master blender has traditionally sat somewhere between artist and alchemist. This remains true to some degree: artisanal creativity and a good nose are essential, while a strong memory and head for numbers are equally important. But increasingly there is also a scientific foundation supporting these personal skills.
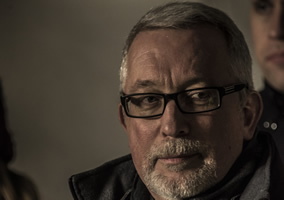
Ron Welsh
Distilleries today balance craft alongside the modern reality of vast warehouses, contemporary machinery, and processes akin to chemical engineering. Beam Suntory master blender Ron Welsh, who says his background in engineering provided a good foundation for his career, sees today’s master blenders operating in a rapidly changing industry: “Innovation is a huge part now. Twenty five years ago each brand had two or three expressions; now it is fifteen or twenty.”
As a result, the master blender must have a true passion for, and a detailed understanding of, the components that affect a spirit’s flavour and development – along with the creativity to make substitutions when ingredients are unavailable. And given the extensive maturation periods, patience is of course a must.
The sheer scale of modern operations is driving change in blending: there’s a great deal to keep track of in the wood alone: a spirit’s colour, flavour and feel will be impacted by what the barrel has been filled with over its lifetime, how many times it has been filled, the wood itself and its charring.
And then consider the fact that modern warehouses store tens of thousands of barrels under a single roof. At such scale, master blenders need more than a sharp memory: they must be able to account for each of the many intricacies that affect finished product – for this it is critical to have access to supporting technology.
Market challenges
Modern distilleries don’t only contend with other brands and producers; they also compete with other spirits. Ron Welsh comments that “Consumers aren’t loyal to brands in the way they once were. Modern customers may want several different drink experiences through a single evening.”
Though there are challenges here, there is also huge potential – as shown in the market’s healthy growth. According to the Financial Times, 2017 saw exports rise 9% in value, and between 2018 and 2023, the whisky market is expected to expand at a compound annual growth rate of 5.3%.
All of this means a requirement for more barrels and greater warehouse capacity – often across multiple locations, which presents additional logistical challenges. As production volumes increase, so too do the number of variables that must be tracked. And of course, when huge production investment decisions are made, it is vital that the data informing them is reliable and accurate.
Technology’s role in the master blender’s toolkit
Today’s master blender must be able to respond creatively to trends, developing true-to-brand blends for consistency, while experimenting with flavours to create different drinking experiences. Both methods require precision, and increasingly – rich data.
Meanwhile, personnel throughout the distillery rely on open communication with the master blender to plan and carry out production, and with so many variables, you can only perform as well as the information to hand. Without knowing exactly where a required barrel is, warehouse managers and picking operators can waste hours tracking it down.
When the bulk stocks manager and warehouse manager receive the master blender’s instructions, they determine which ingredients must be picked and plan work schedules for their staff. Their team may be able to locate the barrels they need quickly, but they may also need to dig out and relocate several layers of casks to reach them. This can lead to increased overtime and unforeseen delays, which impact on the production process.
For this reason, technology is an increasingly important part of the master blender’s toolkit, ensuring information is accurate, up to date, and available to all who require access. But most critically: given the many variables that provide cask maturing spirits their distinct character and flavour profile, is there sufficient data – and detail – to enable the master blender to make fully informed decisions?
Distillery data must be rich, smooth and flowing
By improving how data is managed across the business, information can flow seamlessly between teams while providing detail that will enable efficiency, and the artistry and precision that quality products demand.
Today, some of the industry’s finest blenders rely on industry-specific technology to help them produce their finest whiskies. At Beam Suntory, Ron uses an industry-specific inventory management system to aid his work, and to help throughout the distillery: “It allows me to quickly analyse the stocks we have and what we can use it for; and allows us to easily allocate to future blends.”
Ron believes that data is fundamental to how the distillery plans for the future: “The decisions we make define what we produce; when we need to expand; when we purchase land and build warehouses; and how much to invest in casks,” he says. “It’s a lot of money, so we have to get it right.”
In the past these types of systems tended to be developed in-house, but as the industry evolved the complexity increased, and some producers found their software demanded as much attention as their spirits. Thankfully, there are also industry-specific solutions available that enable distilleries to manage their data without doubling up as developers.
Conclusion
Implementing any new technology is a significant investment. However, it is increasingly clear that reliance on traditional alternatives – paper, spreadsheets, or generic ERP systems – is holding some master blenders back.
Managing spreadsheets is time consuming and notoriously error-prone, and if the accuracy of data cannot be relied upon then its value is questionable. Additionally, this approach tends to lack the required precision: master blenders often have a view of overall stock levels, but no visibility regarding month-by-month maturation.”
While some have embraced Enterprise Resource Planning (ERP) software to help the distillery run smoothly, these systems rarely record sufficient detail to ensure master blenders and their teams can record and recall with the required precision. ERP systems are most effective when integrated with inventory management software specifically designed for distilleries.
There is little doubt that the right technology will help the master blender and the entire distillery to thrive in an ever-changing market. Many distilleries have already improved data input through barcode scanning tools and technology to manage cask filling, but it is increasingly clear that software can help with the storage, management and sharing of valuable data right across the business.
Armed with this data, operations teams save time and become more efficient, while master blenders can focus on providing the artistry and precision that quality whiskies demand.
For a complete overview of the DRAMS solution and its suite of modules, visit our DRAMS overview page here. Here you can learn more about the tools and systems available to support the modern master blender.