However, when it comes to choosing a labelling system you have a number of options, and while our DRAMScan system will happily work with any of them, it is important to understand the advantages of each – and be in a position to choose whichever is best for you.
This guide briefly covers the available options, but if you would like to discuss this subject in more detail then please get in touch.
Consideration 1: Types of Codes (Barcodes Vs QR Vs RFID)
An introduction to Barcodes
The Barcode is the oldest technology of those covered here, but its longevity is testament to its efficiency and effectiveness.
A Barcode is a set of lines of varying widths and heights which, when scanned with a barcode scanner (typically a laser), returns the item code which corresponds with (in the case of maturing spirit) the contents of the barrel.
Barcodes are widely used for barrel labelling in Scotch Whisky production, and there is even a Scotch Whisky Association (SWA) standard for the content of the barcode, consisting of the SWA make code, production year, rotation number, cask number, and filling location. An example of a label conforming to this standard can be seen below.
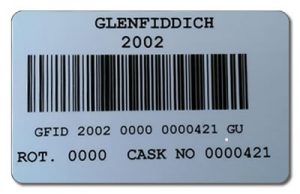
Of course, the labelling of barrels is only part of the story. For ease of data entry, it is common to apply location barcode labels to the end of each level in a racked warehouse. And if a rack can be accessed from either end then both level ends should be labelled; one with a “Front” indicator, and the other “Back”. An example of such a label can be seen below.
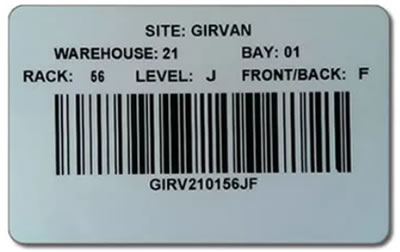
Palletised warehouses present something of a challenge where location labelling is concerned, simply because there is nothing to attach the labels to. The most common solution is to use a book of barcode labels – typically one label per stack of pallets – that can be scanned by the operator when moving pallets into position.
Barcodes are relatively cheap to produce and can be printed internally, though you should note the following section which covers printing processes. Barcode labels also have the additional benefit of being able to incorporate supplementary information (for example the type of spirit), allowing warehouse operators to easily read cask labels with or without a scanning terminal.
The main disadvantage of Barcodes is the limited amount of information that can be stored on each code. The upper limit is 43 characters, but the more characters encoded, the wider the barcode and the more difficult it becomes to scan.
In practice, barcodes tend to be limited to around 20-25 characters. However, neither barrel nor location barcodes exceed this number of characters, so in reality this limitation isn’t much of an issue.
An introduction to QR Codes
You have probably seen QR codes (abbreviated from ’Quick Response Code‘) on adverts, at bus stops and so on. The QR is a type of barcode – albeit one that looks more sophisticated, and needn’t be scanned ‘head-on’ in the way a barcode must.
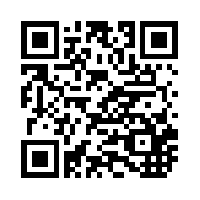
QR codes are often referred to as two-dimensional (2D) barcodes, whereas standard Barcodes are referred to as one-dimensional (1D).
The main difference between a QR Code and a Barcode is the amount of data that can be incorporated: A QR Code can store up to 7,000 characters – though of course it is worth remembering that a SWA cask barcode label only requires 21!
Like a Barcode, a QR Code can be printed internally (again, note the following section on printing processes) – and can be surrounded with supplementary information that identifies the cask contents without the need of a scanning terminal.
The QR Code also has the benefit of redundancy (so not all of the information on the code is required). In practice this means that should the label be partially damaged it is possible it may still be successfully scanned.
Finally, it is worth noting that QR Codes require a different type of scanner to standard 1D barcodes. Standard barcodes can be read with a laser, whereas 2D barcodes require a specific type of scanner, called a 2D imager. The imager takes a picture of the code and analyses the picture to decode the information.
2D imagers are capable of reading both 1D and 2D codes, but often have a shorter range than traditional laser scanners, so the operator needs to be closer to the label being scanned.
Current intrinsically safe scanners can be supplied with either a 1D Laser or 2D Imager, and will support varying read distances (up to 15 metres in some cases). We would advise you to always consider the cost and read-range of each of the options available when selecting a device.
While many see QR Codes as an improvement over Barcodes (largely because they are modern and popular as marketing tools), if you don’t need the additional information they can provide, there may not be significant justification for adopting QR over Barcodes.
An introduction to RFID
RFID stands for Radio Frequency Identification. As is suggested by the title, RFIDs are not merely codes to be scanned; they consist of a transponder and reader, with information transferred via radio waves.
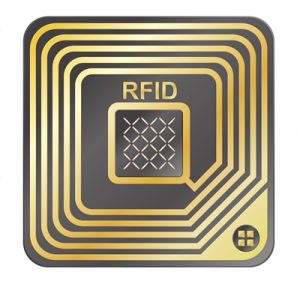
A common advantage of RFID over Barcodes and QR Codes is that scanners can communicate with multiple tags at the same time, but it should be noted that this is not suitable for accurate positional data.
RFIDs have the advantage that they don’t need to be pointed directly at the RFID tag to receive a signal, and they also tend to be small but tough enough to withstand damage – and a tag won’t wear out or deteriorate over time (which is possible with Barcodes and QR Codes if the labelling is not sufficiently durable).
The main problem, of course, is financial: though RFID costs are falling, implementation costs will almost certainly be higher than with either Barcodes or QR Codes. Note that it is difficult to accurately compare costs here, since RFID costs will vary significantly depending on the number being sourced.
Finally, RFIDs lack the immediacy and convenience of internal production, and it is worth noting that RFID has been known to suffer from scanning interference in areas where there is a lot of liquid (like, say, a distillery warehouse!) – though there are ways to address this.
Consideration 2: Printing Methods (for Barcodes and QR Codes)
OK, so you have looked at the available labelling options and decided you want to use 1D or 2D barcodes. Now you just need to print labels that will scan accurately after many years of storage in a distillery warehouse!
While the section above outlined three different options – each with their own merits – when it comes to printing labels for maturing spirit we are firmly of the opinion that you should use a process called ‘Thermal Transfer’.
Why Thermal Transfer?
A key requirement of cask labels is that they must be capable of surviving for extended periods of time in a distillery warehouse.
It is worth noting that both the label substrate (i.e. the surface on which the label is printed) and the printing process itself will affect the durability of the labels.
The range of available printing options can be confusing, but ultimately there is only one print method that provides the print quality and durability needed – and that is Thermal Transfer.
Furthermore, it is essential that full resin ribbon be used with the thermal transfer printing process to ensure a long lasting image. Finally, a synthetic label substrate (e.g. polyester) will ensure that the label is resistant to water, chemicals, and extreme temperatures.
Which Printer?
There are a variety of thermal printer options on the market which are capable of producing cask labels, and they vary in terms of throughput and resolution. For standard barcodes of the size used on cask labels, a print resolution of 203 dpi is adequate.
The number of casks being filled dictates the level of throughput required. Most “desktop” thermal transfer printers are capable of generating several hundred labels a day, but for larger operations it may be worth considering a ‘tabletop’, or ‘mid-range industrial’ printer, which is more suitable for higher production levels.
Should I Buy Pre-Printed Labels?
Use of a label production service is certainly worth considering if you are filling a large number of casks with the same spirit. For example, if you plan to fill 10,000 barrels of Grampian Grain over the course of 2016, why not buy in 10,000 pre-printed labels with the same make, fill year, filling location, and sequential cask numbers from 1 to 10,000?
While the pre-printed approach can reduce the manual overhead of label printing, the ongoing cost will be greater than printing your own labels – even if you avoid purchasing your own printer. In reality, whether you purchase pre-printed labels or not, it is almost certainly worth having a dedicated barcode label printer on site for those situations (e.g. replacement labels, alternative spirits) for which you won’t have pre-printed labels available.
Conclusion
The decision as to which labelling options and scanning technology you adopt is entirely up to you – but we hope this guide has provided the information you require to make the right choice for your organisation.
The DRAMS Scan cask scanning solution is fully integrated with the DRAMS Distillery Management system, and is compatible with Barcodes, QR Codes and RFID tags.
DRAMS are a reseller of intrinsically safe barcode scanners, and we would be happy to discuss your scanner requirements with you in detail.
We do not supply printers or printer consumables directly, but we can offer advice on cask labelling and would be happy to put you in contact with suppliers who provide printers, consumables (print heads, labels etc.) and pre-printed labels to other DRAMS customers.